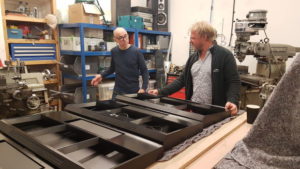
Studio solutions team Frozen Fish Design talk Abbey Road, Twickenham Studios and the Teletubbies
Phil Ward paid a visit to Frozen Fish Design, a Surrey-based studio solutions team that knows how to cut corners…
What do Goldfinger, Abbey Road, green motoring and The Teletubbies have in common? Don’t even bother trying. Naturally, it’s the innovative output of Frozen Fish Design (FFD), a Surrey-based consultancy beyond category. It has made: camouflaged loudspeakers for the lobby of a retro City of London luxury hotel, whose vault was used in a Bond movie; part of an interactive exhibition that illustrates how hydrogen can be used as motor fuel; a Tubby Car, a Tubby Spinny, a Tubby Uppy Downy and a Tubby Slidey for the set of the children’s TV favourite; and a bespoke mixing console for the famous recording studio. Plus, as we all know, Abbey Road is where Tinky-Winky, Dipsy, La-La and Po recorded Sgt Pepper.
It makes sense, then, that FFD’s activities are divided by the company into the following broad areas of activity: collaborative display systems; promotional and interactive installations; film, TV and commercials; and mixing console customisation. These areas have to be broad, because this is a place where anything can happen. The co-founders’ sense of the surreal – the name refers to the partnership of Allan Frost and Glenn Haddock – must come in handy every day.
Hot property
By the universal law of one thing leading to another, the mixing console customisation bit has emerged as a significant business for FFD. Specifically, relationships with Avid and AMS Neve have been established that enable and encourage the combining of their hardware into hybrid chassis and surfaces, along with copious ancillary studio puzzle-solving and space management.
The customer receives all the assistance needed on site to dovetail the chosen solution into each individual space, including any extra modifications needed to get square pegs into round holes, or even to create brand new studios based on the premise that mixing architecture from more than one single manufacturing brand can and will work to the most idiosyncratic specifications. The project is carried through by FFD all the way from design and drawings to assembly and finishes, and the industry is starting to notice.
At the moment the FFD catalogue illustrates proven adaptations of AMS Neve DFC and Euphonix System 5 consoles to include Avid S6 control surface modules, but these might only be the beginning. The company also offers bespoke console accessories, extensions and other technical furniture that will enhance workflow in any shape or size of music recording or audio post-production facility. This includes many and varied gizmos, from removable module enclosures and shelving to mouse-and-keyboard platforms, mouse-and-keyboard panels, screen sliders, static screen mounts, MIDI keyboard panels, support frames and legs.
The workshop is not a million miles from Pinewood and Twickenham, and there is a heritage. Television provided an initial impetus for a previous generation: the site is where Allan Frost’s father ran his business as a set builder, for which the late, lamented and local Teddington Studios provided much TV work for Thames, the BBC, Channel 4 and many other broadcasters. The walls vibrate with legacy, and it is no doubt a point of honour that Avid consoles are now re-fabricated in the same space as George & Mildred’s living room.
Haddock and Frost met when each worked across this hinterland of facilities – also including Shepperton – with Haddock a prop maker and model builder, among other things, and Frost an early expert in CAD-assisted engineering projects for complex set design and hi-tech production. They saw a future in bespoke solutions for ever-more technical sets and props, and eight years ago decided to start an entirely different kind of agency.
“In our different ways we were both being asked by more and more people if we could make totally unique and unusual things,” Haddock recounts, “not just in media production but also for exhibitions and other types of display. It began to make really good sense to start a company together and address all of these new demands directly.”
FFD’s nimble genre-hopping has been helped by new generations of manufacturing technology, not the least of which is 3D printing. “Design and manufacturing has evolved easier ways to do things,” continues Haddock, “less labour-intensive ways of creating solutions, using software that exports files that other companies can read, and then pump the data into their laser cutting machines, 3D printers or CNC machines.
“It means you don’t have to have every single machine in your workshop – almost like virtual manufacture. You model the ideas in CAD software, up to a complete shape and look, and when you’re happy with what it looks like and what it does you split it up into its component parts and send out those parts to the relevant out-source. All the different tolerances, finishes and paints are then combined into the final product.”
Cash for Gold
Goldcrest Films provided early projects for FFD, as did Twickenham Studios despite its well-publicised difficulties. “Twickenham was about to be taken over by property developers,” Haddock remembers, “but the ‘Save Twickenham Studios’ campaign was successful and all the facilities were upgraded. Audio post-production got a particularly extensive facelift, and we were called in to meet the project manager whom we’d already worked with at the Sky Academy Skills Studios in Richmond.”
The reputation spread, and FFD’s signature solutions began to appear elsewhere in London – not least in a certain NW8 facility. “Some of the designs we did for Twickenham have also gone into Abbey Road,” adds Haddock, although the latter now boasts a unique AMS Neve/Avid hybrid that extends the FFD proposal to hitherto unrelated brands. One Amsterdam project – an advertising post house with smaller rooms and consoles – keeps it more ‘in the family’ by converting the facility’s Euphonix System 5 to accommodate an Avid S6 control surface, Avid having absorbed Euphonix into its DNA. “Either way, it saves having to junk your console,” as Haddock points out. “It’s a very modern and hi-tech piece of recycling! This hardware can become worthless very quickly, but it can be re-purposed. You don’t have to throw it away, or try to sell it on the open market for an ever-decreasing return on your investment.”
The manufacturers themselves appear to support FFD’s machinations wholeheartedly, and are only too happy to share the blueprints in order to lengthen the shelf life of one component or another. “Pro audio is almost like a global small business, in which despite the distances everyone knows one another,” says Haddock. “It feels like people in it are willing to share and contribute, and more often than not they’ve worked together at some point. There is competition, but there’s also a sense that businesses complement each other and share a good deal of respect.
“What we’ve found with AMS Neve and Avid is that the benefits of our hybrid solutions are well appreciated. It opens up the market among facilities where they wouldn’t otherwise have had access, and provides a completely new upgrade path. It also re-invigorates interest in workflow. There’s no one, set way of doing anything these days and we’re going down paths no individual brand could take.
“It also dramatically increases their attraction in the dry hire space, where rooms can be configured completely differently every time. You no longer have to search around for the fixed space that will accommodate you, or compromise on your choice of mixing platform, or be forced to start in one facility and finish in another.
“We noticed very quickly that dubbing mixers and sound designers are becoming like rock stars – they’re Oscar-winning people! You need them on board if you want a film to be successful, and they now represent quite a powerful lobby. We got such a positive reaction from our initial work at Twickenham that I’m sure it gave the guys from AMS Neve and Avid the confidence to support what we do.”
Joint enterprise
In practice, Frozen Fish Design represents a complementary sales and marketing effort. It’s only a matter of time before others notice the advantages of this strategy.
“The principle could be applied to any architecturally compatible equipment,” says Haddock. “The S6 design is modular, so it’s perfect for this kind of adaptation. The DFC has modules, but each module is plugged into a circuit board mounted within the basket so it’s not quite as flexible. The S6 is state-of-the-art and very popular, so that’s the one we’re having success with when we apply this integrated approach. I’ve been asked to look at other consoles, including SSL, but the question is whether we can get an S6 to fit the chassis. People are beginning to make these enquiries, because they’re interested in using both systems.”
And the limits to this jigsaw are purely physical, Haddock stresses. “Audient is another suggestion we’ll be looking at, and the S6 control surface remains the most viable option to date. We haven’t had requests for any other combinations yet, but who knows? There’s no reason why other consoles can’t be re-purposed to mix and match anyone’s favourite ingredients. It’s about dimensional constraints: if you’ve got a space that something needs to go into, does the chosen solution fit those dimensions? If loosely it does, the structure that supports it can be worked on to suit. It’s making people think about other ways of upgrading a facility or service. The ergonomics are being reinvented at the front end, not as the final piece of the equation, and you can really start considering building the console around the space rather than building the space around the console.”
Source: mi-pro.co.uk